Absorption Costing
What is Absorption Costing?
The absorption costing method includes all production costs—both variable and fixed.
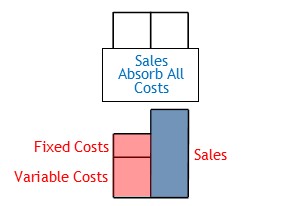
How it Works
Suppose a manufacturer has a contract to build 30 work stations over three quarters.
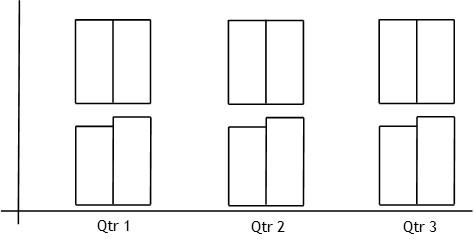
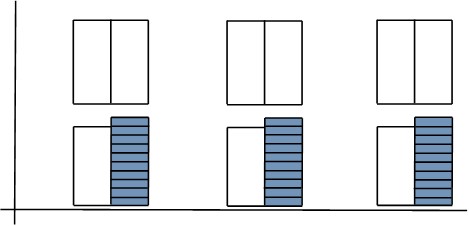
Variable Manufacturing Costs
Some of the costs involved in the production of the work stations will be variable costs.
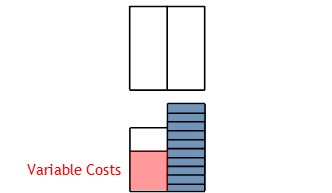
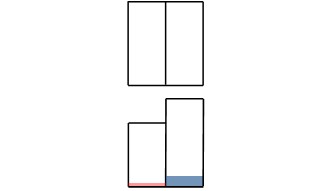
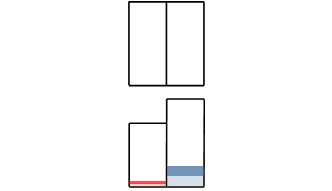
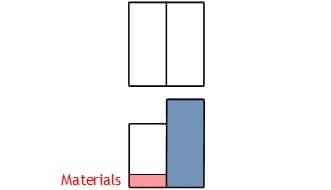
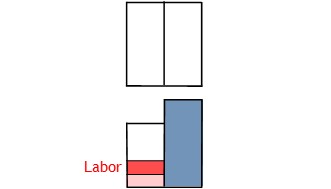

All up, these are the costs that make up the variable component of production costs.
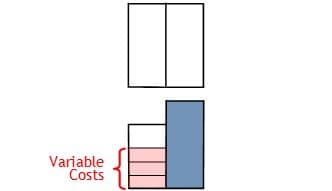
Fixed Manufacturing Overheads
If total costing accuracy is required, each unit sold should absorb all production costs.

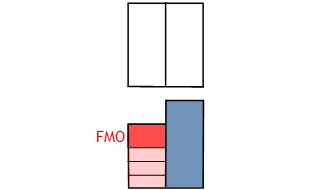
Fixed manufacturing overheads are period costs.
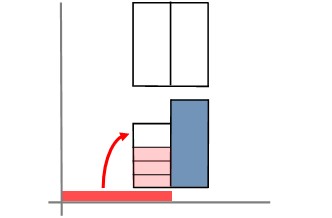
They include things such as factory or corporate office rental.
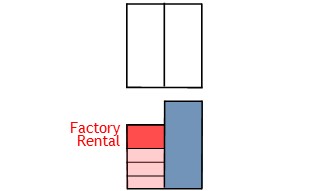
FMO costs are incurred at the same level, regardless of whether or not the manufacture makes sales.
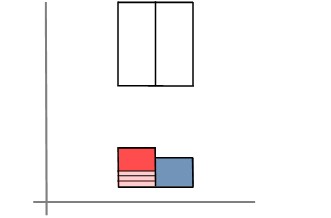
Absorption Costing Method
With the absorption costing method, you begin by taking total FMO for the period.
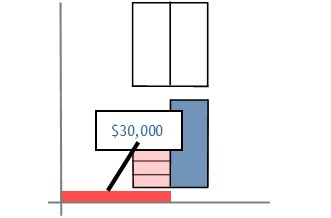
Then you divide this by the total number of units produced.
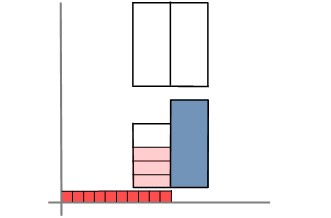
In this example, first quarter production was 10 units.
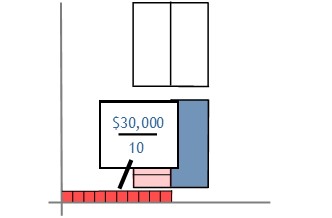
So by dividing total FMO by 10, you see how much it cost to produce a single unit.
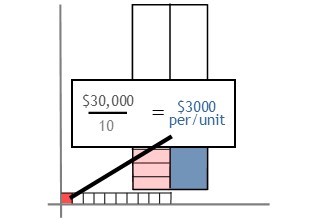
Next, you multiply unit FMO by the number of units delivered or sold.
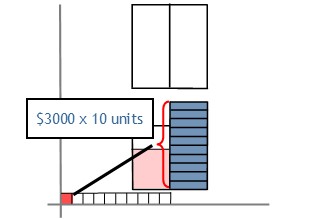
Doing this will apply fixed manufacturing overhead to sales for the period.
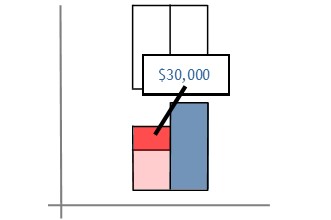
Disadvantage of the Absorption Costing Method
By accounting for all production costs, you will establish an accurate costing for the units sold.
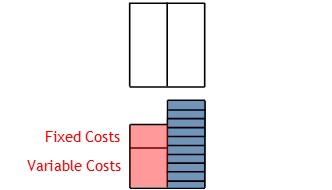
The problem is, the absorption costing method can skew the picture of a company’s profitability.
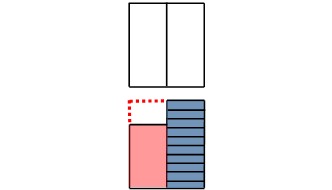
For example, if the manufacturer has identical sales and costs in each of the three quarters, all costings should be the same in each quarter.
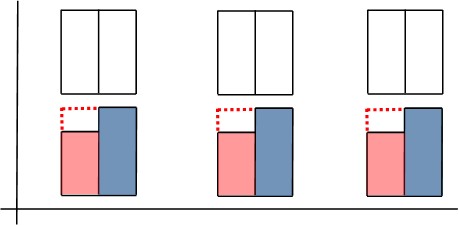
With the absorption costing method, this is not necessarily the case.
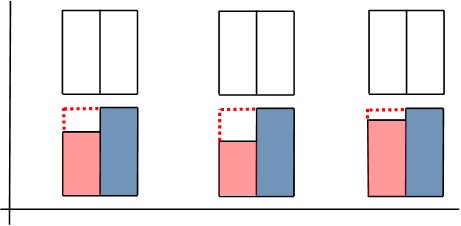
In the example shown thus far, all the units produced in the quarter were delivered in the same quarter.
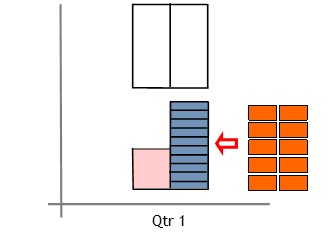
Not all quarters work the same way, though.
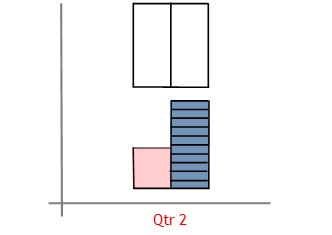
For example, in the second quarter, the manufacturer may produce fifteen units.
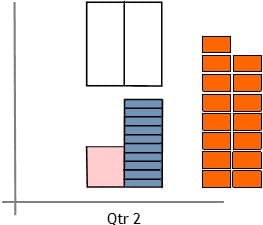
In this case, they will still only deliver ten units to the customer.

The excess production of five units is held in inventory.
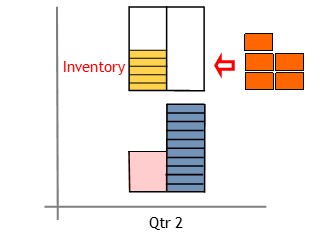
To find FMO per unit sold, you once again take total fixed manufacturing overheads for the period.
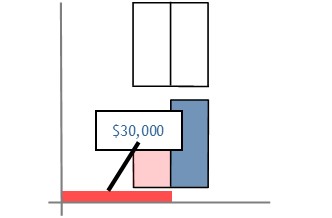
Only this time, you divide that amount by 15, the number of units actually produced this quarter.
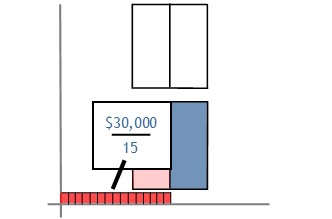
This will show FMO per unit produced in the second quarter
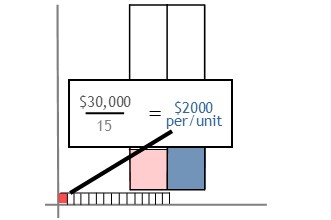
Unlike the first quarter, you don’t assign the entire FMO to sales,
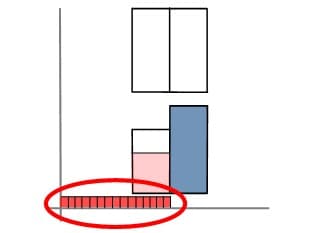
Only 10 of the 15 units produced were delivered to the customer.
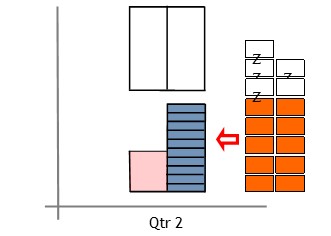
Therefore, you only assign a commensurate portion of FMO to the units sold or delivered.
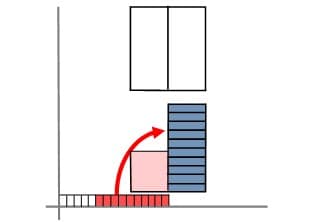
To make the calculation, you multiply the FMO per unit by the number of units sold.
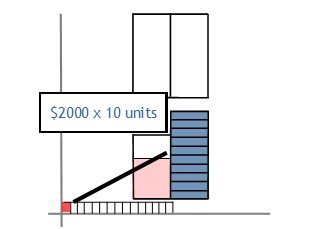
Once calculated, you will notice that second quarter FMO is lower than that of the first quarter.
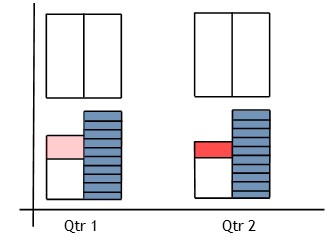
This, however, will be offset in the third quarter.
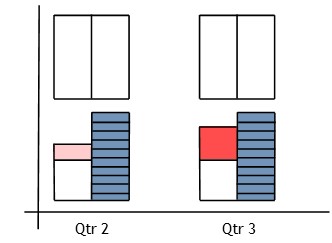
In the third quarter, the manufacturer will deliver ten units, as usual.
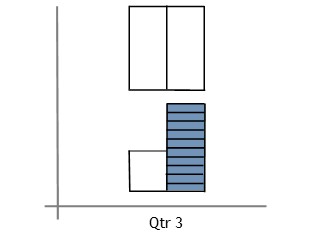
However, they already have five units in inventory.
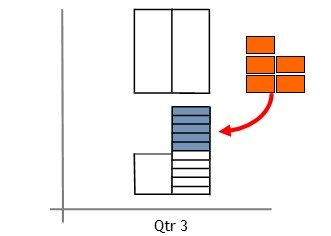
So the manufacturer will only need to produce five units during the quarter.
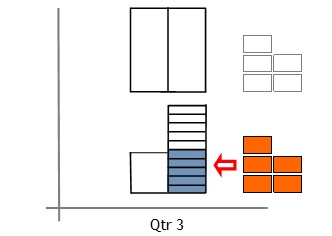
Despite this, the FMO period cost is the same as in all other quarters.
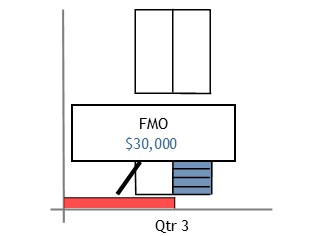
This means the FMO costs will be spread over 5 units only during the third quarter.
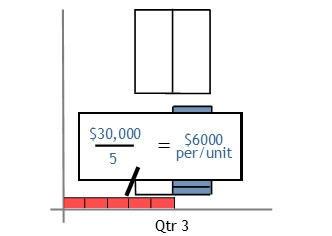
Once calculated, you will see that the final quarter FMO is higher than that of the second quarter.
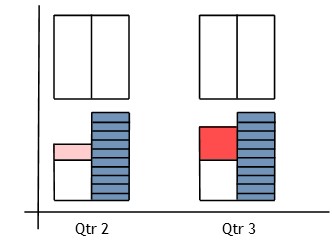
This offsets the diminished costing shown in the second quarter.
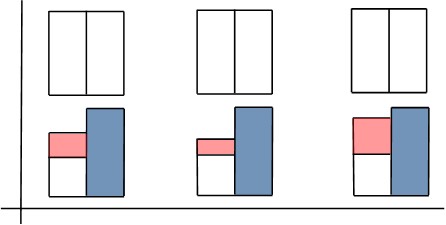
So in the end, the final result is the same as if all quarter’s costings were identical.
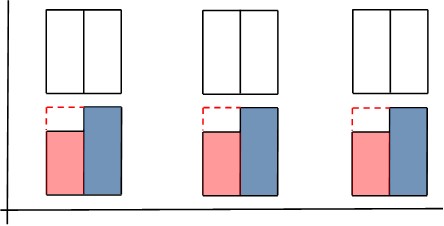
However, the quarterly financial reports will make it appear otherwise.
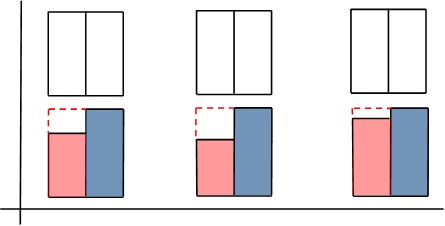